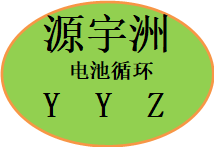
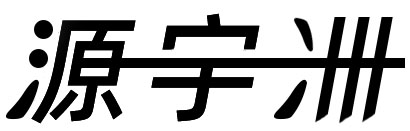

锂离子电池极片的微观结构受到制备工艺的影响,又直接决定电池的最终性能,电池极片微观结构的优化至关重要电池极片是一种多孔复合材料,其微观结构示意如图1所示,
包括至少4个区域:
式中,φAM为活性物质相体积分数,φCA为导电剂相体积分数,φB为粘结剂相体积分数,ε为极片孔隙率,即电解液相体积分数。导电剂和粘结剂相互混合在一起,很难区分。
锂离子电池极片涂层中,孔隙是重要的结构特征,填充满电解液,成为锂离子传输的主要通道。极片涂层中多孔结构特征,具体包括孔径大小与分布、喉道尺寸、连通性和迂曲度等重要参数,均与锂离子的传输特性密切相关。
孔隙率是指电极涂层中孔洞所占体积分数,可通过涂层的体密度,涂层各组分质量百分比和涂层组分真密度来计算得到,由式(2)表示。
(2)
式中,ε为极片涂层孔隙率,ρcoat为涂层体密度,ω为涂层组分质量百分比,ρ为涂层组分真密度。下标AM、CA、B分别表示活性物质、导电剂和粘结剂。锂离子电池极片中一般存在多种尺度的孔隙:1)活性物质颗粒之间的微米级孔隙;2)活性物质颗粒内部的孔隙,尺度为纳米-亚微米级;3)导电剂和粘结剂混合相内部的纳米尺度孔隙。电解液填充在多孔电极的孔隙中,锂离子在孔隙内通过电解液传导,传导特性与孔隙率密切相关。孔隙率越大,相当于电解液相体积分数越高,电解液浸润就越充分,有效锂离子电导率也越大。而正极极片中,电子通过碳胶相传输,碳胶相的体积分数和碳胶相的连通性又直接决定电子的有效电导率。孔隙率和碳胶相的体积分数是相互矛盾的,孔隙率大必然导致碳胶相体积分数降低,因此,锂离子和电子的有效传导特性也是相互矛盾的。随着孔隙率降低,锂离子有效电导率降低,而电子有效电导率升高。因此,孔隙率的优化是电极设计的关键。Jiang等采用晶格玻尔兹曼模型,模拟了电子和锂离子在多孔电极中的传输过程,重点考察了颗粒尺寸,极片孔隙率对电子和离子传输的影响。结果表明,小颗粒和大孔隙率的正极极片,以及大颗粒和小孔隙率的负极极片能够提高电池高倍率性能和活性物质利用率。商业化锂离子电池极片孔隙率一般为20%~40%。
近年来,提高能量密度成为发展锂离子的重要方向。电极工程方面,制备高涂布量的超厚极片是提升电池比能量的一个最直接的办法,而厚极片中锂离子在电解液中的迁移阻力增加是影响倍率特性的主要原因,特别是当电解液能够浸润的深度小于极片的厚度或与极片厚度相差不大时,锂离子在极片内的扩散过程受限,电解液通道成为影响电化学过程的主要因素。Chen等采用多物理量的有限元模型模,主要从电子导电率、离子导电率、比能量等方面优化了极片的孔隙率和极片厚度。并提出,对于厚极片(250~400μm),锂离子长距离的扩散是限制因素,需要采用高孔隙率的极片设计策略。
针对硅基负极,需要考虑硅基电极在充电过程中的体积效应。Heubner等从理论计算上优化硅基极片孔隙率和厚度,由于充电过程中硅基材料体积膨胀会填充电极中原本的孔隙而降低孔隙率,为了避免由此引发的电极颗粒接触产生剧烈的变形和应力,以及孔隙率剧降造成的电解液锂浓度低等问题,电极初始孔隙率存在一个阈值,电极设计时,孔隙率必须大于此值。因此,在硅基负极设计中,极片应该比石墨负极具有更大的孔隙率,甚至高达60%~70%,高孔隙率能够缓冲硅基材料的体积膨胀,限制极片的变形,减缓涂层从集流体脱落。Zhao等实验验证了硅基负极孔隙率增加可以提升电池性能,他们在浆料搅拌阶段将NaCl加入SiO电极浆料中,在其它条件相同的情况下,电极性能明显优于传统方法制备的电极,在100个循环后容量依旧维持在3mA·h/cm2以上。这是由于加入10%的NaCl能够产生足够的内部孔隙,从而稳定了电池的循环。电极中活性物质的体积膨胀阻碍了离子传输,增加孔隙率能够促进锂离子的传输以及给SiO预留一定的膨胀空间,从而提高了电极的机械稳定性。
为了进一步提升电池的能量密度和功率密度,从锂离子电池电极反应动力学过程出发,研究者们更加精细地设计极片的微观结构。从集流体到电极表面孔隙率逐渐提升的电极不但能够保证足够的离子扩散速度,还能保证良好的电子传导特性。Subramanian等采用数值计算的方法优化极片厚度方向的孔隙率分布,他们将极片沿厚度方向分成 N段,分别设计每段的孔隙率,降低极片的电阻。结果表明,从集流体到隔膜孔隙率逐步升高,当N=5时,与单一恒定孔隙率为0.4相比,极片离子电导率性能提高17.2%,与单一孔隙率0.2相比,性能提高4%。如果继续增加极片厚度方向的分段数N来优化孔隙率,电极性能提升少,而极片实际制备工艺难度增加。Golmon等和Dai等基于数学模型分析发现,随着电极活性物质装载量和倍率增加,电极极化现象加重,而梯度孔隙率的电极设计能够有效降低极化程度,提升能量密度。最近,Du等也采用伪二维电化学模型模拟了极片厚度方向孔隙率分布函数对电池比能量的影响,研究结果也表明孔隙率在正极厚度方向的梯度分布优化能够提升电池比能量。
孔隙率梯度电极优化的实验验证方面,通过采用不同的活性物质形态可以实现孔隙率的控制。如一般活性物质颗粒尺寸减小,则涂层体密度增加,孔隙率会更低。活性物质的粒径分布也会影响电极的孔隙率,活性物质颗粒的粒径呈现多峰分布时,电极孔隙率要低于呈单峰分布的活性物质颗粒。另外,通过在电极浆料中加入添加剂改变材料的团聚状态也可以调节电极的孔隙率。利用上述方法,通过多层电极工艺就能够实现电极孔隙率梯度分布设计,从而在保证功率密度的条件下提升电极能量密度。Huang等采用超音速悬浮液雾化和自动喷涂沉积工艺制备双层涂层,首先在集流体上制备一层厚度约6.1μm的多孔钛基材料涂层,材料粒径约200nm,孔径40 nm。然后再在上面沉积一层无孔钛基材料。多孔TiO2内部孔洞有利于锂离子的扩散,从而提高倍率特性,但是如果全部使用多孔颗粒,电池体积能量密度很低。双层电极结构能够同时保证高体积能量密度和高功率密度特性。Bitsch等则在浆料中加入辛醇,使得炭黑导电剂表面张力减小、更容易团聚,涂布电极的孔隙率从53%提高到了66%。实验中他们首先喷涂一层常规浆料,之后直接在湿浆料涂层上二次涂布加入辛醇的浆料,所形成的的双层电极孔隙率不同,结合高孔隙率电极的优势,同时也获得了较高的电极质量密度,提升了电池的能量密度和比能量。
多孔电极中,除孔隙率之外,孔隙迂曲度也是与传输特性相关的一个重要参数。有效扩散率、传导率等 Deff输运物性的关系可用式(3)表示:
(3)
式中,D0表示材料本身固有扩散(传导)率,ε为多孔电极中的孔隙率,τ为孔隙的迂曲度。多孔介质中,如图2所示,将两点之间实际传输路径长度Δl与直线距离Δx比值的平方定义孔隙迂曲度,表达为式(4):
(4)
图2 多孔介质传输迂曲路径二维示意图
在宏观均质模型中,一般采用Bruggeman关系式(5)表示,取系数α=1.5来估计多孔电极的有效物性。
(5)
而实际的锂离子电池多孔电极中,孔结构并非均匀分布,结构和形态复杂,很难直接测量得到孔隙迂曲度。为了获取真实的孔隙特征,研究者致力于开发高效快捷的迂曲度测量方法,修正宏观均质模型中描述孔隙迂曲度的Bruggeman指数。Ebner等从X射线断层扫描重构3D电极结构中发现了孔隙的局部不均匀性,结合X射线成像技术分辨活性物质相的特点,把电极的孔隙迂曲度分为活性物质相和非活性物质相形成的迂曲度,整个电极的迂曲度是两者的乘积,假定非活性物质相的迂曲度遵循Bruggeman关系,而活性物质相的迂曲度直接从3D结构数据计算。基于微分等效介质理论,他们还开发了一个软件专门快速评估锂离子电池极片的孔隙迂曲度。输入电极表面和横截面两张扫描电子显微镜照片,软件通过分析每个活性物质颗粒的a、b、c三轴的数值和分布状态计算迂曲度。Dubeshter采用气体输送阻力测量方法测定锂离子电池正负极极片的孔隙迂曲度,并发现实验测量的迂曲度明显比Bruggeman关系描述的高很多。Cooper等和Vadakkepatt等将实验重构的3D电极微结构网格化后,利用流体力学模拟多孔电极的热交换来计算孔隙迂曲度。而Chen-Wiegart等[59]则直接在FIB-SEM重构的3D电极结构中测量孔道实际长度来计算迂曲度。
锂离子电池多孔电极的孔隙迂曲度还存在各向异性。Ebner等制备了球形NMC颗粒、椭球形LCO颗粒和片状石墨3种电极,然后采用X射线断层扫描成像技术重构电极微结构,通过扩散模拟计算得到平行于集流体的x和y轴方向以及垂直于集流体的z轴方向的孔隙迂曲度与孔隙率的关系曲线,如图3所示。从图3中可见,球形的NMC电极,3个方向迂曲度指数一致,迂曲度各向同性;而对于非球形颗粒电极,z轴与x、y轴表现出各向异性,迂曲度更大,而片状石墨z轴迂曲度差异最大。SEM观察电极形貌发现,在常规工艺过程中片状石墨倾向于平行于集流体方向分布,堵塞了孔隙通道,造成了z轴方向迂曲度大。而锂离子电池离子传输方向主要是垂直于集流体的z轴,因此,非球形的活性物质颗粒电极离子传输阻力大,电池倍率性能差。
图3 迂曲度与孔隙率的关系
锂离子电池极片中离子主要在垂直于集流体的z轴方向上传输,而传统工艺制备的电极往往在这个方向迂曲度更高,限制了锂离子的传输速率,而且随着极片厚度增加时,锂离子传导距离增加,考虑到孔隙率和孔隙的曲折连通,锂离子在孔隙内的迁移距离比极片厚度多出很多倍。研究者们对锂离子电池极片微观结构进行设计,电极内部包含垂直于集流体的孔道,在z轴方向降低迂曲度,提升锂离子的有效扩散系数和电解液浸润程度,从而提升电池的倍率性能和活性物质利用率。Chiang等设计了一种包含垂直孔道的电极以降低迂曲度,如图4所示。经过孔道直径和间距的优化,通过计算发现这种结构能够有效降低迂曲度,提高锂离子有效扩散系数。Mohammadian等采用数值模拟的方法证明了这种包含垂直孔道的电极能够有效改善电解液的浸润性,提高活性物质利用率并降低热失控风险。基于这种结构,Chiang等分别采用挤压烧结法、电极浆料定向冷冻法和磁场控制涂布法制备了LCO和NCA电极,电极面容量可达到12mA·h/cm2,是传统电极的3倍。Billaud等采用磁场控制涂布法制备了片状石墨负极,使片状石墨垂直集流体排列,降低孔隙迂曲度4倍,提升了电池的倍率性能。俞书宏等利用自然界树木的导管结构,制备了一种具有垂直微孔结构的超厚LCO正极,降低了电极孔隙的迂曲度,从而降低锂离子在电极内的传输阻力,在高负载量的情况下也能够保证电池的循环性能和倍率性能。LCO的负载量最大可达160 mg/cm2左右,是传统工艺的4~5倍。
图4 活性物质颗粒多孔电极基体上的周期孔道阵列
1)导电剂均匀分散,在活性物质颗粒表面形成导电薄层;
3)导电剂之间相互连通导电,从集流体到每一个活性物质颗粒形成电子通路。
导电剂在电极中的作用是提供电子传输的通道,导电剂含量适当能获得较高的放电容量和较好的循环性能,含量太低则电子导电通道少,不利于大电流充放电,会导致电极中活性物质利用率低;太高则降低了活性物质的相对含量,使电池比能量降低。
导电剂的形态和种类众多,颗粒状炭黑和导电石墨是零维结构,而碳纤维和碳纳米管是一维结构,石墨烯是二维片状结构,导电剂的微观结构特征与分布是影响导电性能的重要因素。细小颗粒状的零维结构的导电剂是点接触、线状一维结构导电剂是线接触,片状二维结构导电剂是面接触。颗粒状导电剂更容易在活性物质颗粒表面均匀分散,与活性物质紧密接触,形成良好的短程电子通路,但是在整个电极的厚度方向不利于形成长程的电子传输通道。而一维结构的导电剂与活性物质难形成紧密接触,短程电子传导差,一维长链结构使长程电子传导性能好。石墨烯具有很高的电导率及二维超薄的结构特征,通过与活性物质的“面—点”接触,使得很少含量的石墨烯就可以有效提高电极的电子电导率,但其分散困难,团聚的石墨烯会对电极内部锂离子的传输产生阻碍,影响高倍率条件下电池性能的发挥。综合利用各种形态导电剂的优点,采用多种结构的混合导电剂有利于形成完整的导电网络。Shi等发现,在LCO正极中,石墨烯与碳黑导电剂混合使用时,只需要1%的石墨烯就能够形成有效的电子传输网络。Bockholt等混合使用纳米碳黑和片状微米级导电石墨,配合合适的电极工艺,碳黑均匀分布在活性物质颗粒表面,形成良好的短程电子传输通道,而微米级片状石墨连接碳黑形成长程导电通道。
导电剂的垂直分布对电池性能有显著影响,合理设计多层结构的电极,有利于同时提高电池的能量密度和功率密度。Liu等采用分次涂敷方法制备了两层结构LFP极片,研究了每一层导电剂含量对电池性能的影响。电化学性能测试结果表明在总导电剂含量5%不变的情况下,靠近集流体的下层导电剂含量高的极片性能更好。如图所示11所示,与上层导电剂含量多相比(图5a),下层导电剂含量更多(图5b)能够形成更多地导电通路,极片电子传输电阻低,电池倍率性能和循环稳定性提升。Chen等使用双层涂布机制备了双层结构的LiNi0.5Mn0.3Co0.2O2正极极片,两层电极浆料导电剂配方不同,一种含有更多的微米级石墨导电剂,而另一种含有更多的纳米级碳黑,对比研究了4种电极结构的电池性能,发现下层含有更多导电石墨、上层含更多碳黑的电极结构所制备的电池具有更高的比容量和更长的循环寿命。因此,多层电极结构成为提升电池性能的一种有效设计手段。
图5 导电剂垂直分布对电子传导影响的示意图
电极中粘结剂一般和导电剂混合在一起,使活性物质颗粒通过碳胶混合相连接在一起形成机械性稳定的整体,并确保电极与集流体之间具有足够的粘结强度。粘结剂分布不均匀会影响电极的机械稳定性,也会导致电池电化学性能劣化,如涂层和集流体界面粘结剂减少会导致涂层结合强度低、循环过程中从集流体脱落而失效。Li等研究了水基和有机物基LCO电极片中粘结剂的浓度分布,并讨论了粘结剂分布对电极物理和电化学性能的影响。当用有机物溶剂制备LCO浆料时,在干燥的电极片中明显观察到粘结剂和石墨导电剂的不均匀分布,而对于使用苯乙烯丁二烯橡胶(SBR)和羧甲基纤维素钠(CMC)的混合物作为粘结剂的水基方法制备的电极片,这些不均匀的组分分布不太明显。Baunach等研究了干燥温度对电极结构的影响,结果显示电池极片的粘结强度与干燥温度存在很强的相关性。在较高的温度下,电池极片的粘结力较低,这表明集流体与涂层之间的界面粘结剂含量发生了变化。此外,研究者也研究了蒸发条件(干燥温度)和粘结剂分子链长度(相对分子质量)对电极涂层的微观结构的影响,以及蒸发速率对粘结剂在电极微观结构分布及电化学性能的影响。
3.4 理想的电极微观结构
从锂离子和电子的传输,以及机械稳定性综合考虑,最理想电极整体微观结构如图6所示:导电剂和粘结剂充分分散,均匀分布活性物质颗粒表面,导电剂相互连通形成电子传输网络,粘结剂分布均匀,确保颗粒涂层的结合强度和机械稳定性高,活性物质颗粒保持原始形貌并分散均匀,整齐排列,形成从电极表面到集流体的垂直孔道,确保电解液充分浸润,实现锂离子的快速传导。
图6 理想的电极微观结构示意图