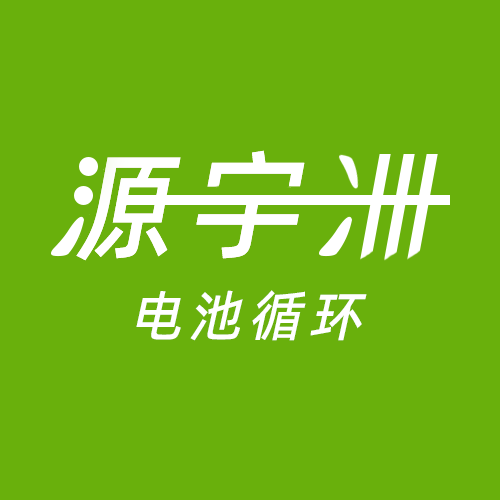
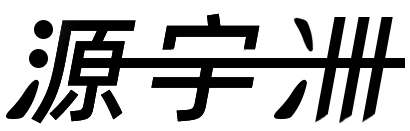

▍研究背景
为了满足现代社会不断增长的能源需求,开发具有高能量密度和长循环寿命的锂离子电池(LIBs)已成为电池研究的关键目标。对于目前商业化的LIBs,负极材料往往采用石墨或硅碳,电池中的活性锂完全由正极材料提供。然而由于负极固态电解质界面(SEI)的形成,现有的LIBs不可避免地存在活性锂损耗(ALL)的问题。ALL不仅发生在首圈充放电过程中,还伴随着电池的长期循环而持续存在,这导致电池能量密度和循环寿命显著衰减。
锂金属的表面贴合预锂化技术被公认为最具商业化应用前景的负极补锂技术。而以往的研究中往往忽视了表面贴合预锂化对电池循环性能产生的负面影响。这些负面影响会降低预锂化所带来的能量密度提升,破坏电池循环性能。因此,探究这些负面影响的产生机制并提出相应的解决策略对锂离子电池负极预锂化技术的应用至关重要。
▍成果简介
近日,同济大学王超研究员团队在国际顶级期刊Energy & Environmental Science上发表了题为“Air-Stable Lithium-Sandwiched Current Collector for Non-Destructive, Thermally safe, and Sustained Supplementary Lithiation”的研究论文。该工作探究了表面贴合预锂化中锂利用率低且电池后期容量加速衰减的原因。针对该问题,该工作制备了一种补锂集流体,实现了石墨负极无损伤的全生命周期补锂,显著延长了LIBs的循环寿命。当应用于磷酸铁锂||石墨(LFP||Gr)全电池时,这种策略使电池表现出优异的电化学性能:在400次循环后表现出高达96%的容量保持率。
▍研究亮点
亮点一:表面贴合预锂化损伤机制探究
以LiAg合金为锂源,该工作探究了表面贴合预锂化全电池后期容量加速衰减机制:预锂化过程中,锂的溶解会阻断锂与石墨之间的电子转移路径,带来石墨表面大量的锂残留,降低了锂的利用率,同时破坏了石墨/电解液的界面稳定性。
亮点二:补锂集流体提供稳定电子转移路径,提高锂利用率
通过简单的热辊轧,该工作制备了含锂复合集流体(Cu/LiAg/Cu,CLC)。石墨与LiAg之间的Cu层作为导电中间层,提供了稳定的电子转移路径,使CLC中LiAg的利用率达到97%。
亮点三:补锂集流体中锂的缓释实现无损伤全生命周期补锂
由于CLC中锂与电解液的接触面积小,锂的释放速率缓慢,在单次循环中释放的锂容量会被及时消耗,CLC补锂全电池的N/P值可以维持1.05不变,提升了电池的能量密度。同时锂残留物会被锁定在集流体中,对电池性能不产生影响。
亮点四:补锂集流体实现热安全的硅基负极补锂
硅与锂金属在辊轧力作用下会迅速发生反应,短时间内产生巨大的热量,对电池生产安全造成极大的威胁。补锂集流体中铜箔隔绝了表面硅与锂源,同时减缓了硅的锂化速度,实现了硅基负极的安全无损补锂。
▍图文导读
表面贴合预锂化损伤机制探究
以超薄LiAg合金箔为锂源(5微米,对应容量为1mAh cm-2),对石墨负极进行表面贴合预锂化。实验结果发现预锂化后石墨负极可拔出的锂容量远低于电化学预锂化(1mAh cm-2)。同时,XRD测试结果中表面贴合预锂化的石墨的002峰的位移小于电化学预锂化,表明表面贴合预锂化石墨的锂化程度低于电化学预锂化。进一步通过SEM对预锂化后石墨电极表面进行观察,发现电极表面存在大量不同尺寸的锂合金碎片。以上结果表明,表面贴合预锂化后,大量活性锂未被吸收,残留在表面的锂合金中。通过原位光镜对锂的吸收过程进行观察可以发现,在注入电解液后,锂开始被石墨吸收。在电解液加入30min内,大部分的锂已经消失,只留下一些残存的合金碎片。这些合金碎片的吸收速度较慢,甚至在经过4h的静置后,仍可以观察到碎片的存在。为了探究表面锂残留形成的原因,该工作对预锂化后石墨负极的截面进行了观察,截面SEM图片显示残留的锂碎片和石墨之间存在明显的空隙。这些空隙的形成是由于石墨和锂合金之间的不良接触导致的。具体来说,由于锂合金表面存在起伏且石墨颗粒呈堆叠状态,石墨与锂合金之间的接触是局部分布的。预锂化过程中,接触点的锂会优先溶解,使石墨和合金之间的电子转移路径被阻断,造成表面锂残留。表面锂残留不仅会降低锂的利用率,同时也会破坏石墨/电解液界面稳定性,造成预锂化全电池后期容量加速衰减。
图1 表面贴合预锂化对电池性能损伤机制探讨
补锂集流体的制备及空气稳定性表征
为了解决表面贴合预锂化存在的问题,该工作将表面锂源放置在集流体中,制备了一种可持续补锂的含锂集流体。如图2a,b所示,将锂银合金箔与铜箔叠成三明治结构,再对复合集流体进行热辊轧以降低其厚度,最终得到不同厚度的补锂集流体(Cu/LiAg/Cu, CLC)。通过对16微米厚的补锂集流体进行形貌观察,发现其表面存在直径约为5微米的微孔,这些微孔是铜箔在热辊轧过程中发生变形形成的。微孔的形成对补锂集流体中锂的释放至关重要。在电位的驱动下,CLC中的锂通过铜箔向石墨中转移电子,同时形成的锂离子通过微孔向电解液中释放,形成了稳定的预锂化回路。图2f,g中CLC的截面SEM表明制备得到的16微米厚的CLC中锂层的厚度约为5微米,且铜与锂之间的结合紧密。由于CLC中大部分锂都被铜覆盖,只在微孔区域接触空气,因此CLC具有优异的空气稳定性。如图2h所示,当LiAg合金在空气(60%RH)中暴露1h后,其表面由银白色变为黑色。相反,即使将CLC 在相同环境下暴露48h,其表面无明显变化。同时,锂银合金和CLC 在空气环境中暴露时的质量变化表明,在初始1h内,LiAg的质量增加达到了109%,而CLC的质量增加只有4%。以上结果表明该工作制备的CLC具有优异的空气稳定性,降低了其规模化应用的环境湿度要求,从而减小了生产成本。
图2 补锂集流体的制备及表征
补锂集流体实现无损伤全生命周期补锂
为了测试得到的CLC的电化学性能,该工作先以NMP为溶剂进行石墨负极涂覆。图3a-c展示了涂覆得到的石墨负极的宏观和微观形貌。可以看出,Gr-CLC与正常石墨电极没有明显的形貌差异,且石墨层与CLC之间的结合较为紧密。进一步,该工作探究了不同厚度的CLC(13微米,16微米和19微米)的电化学性能差异。结果发现,随着CLC厚度的降低,预锂化全电池的首效逐渐升高。首效的升高与不同厚度CLC中孔的尺寸和密度有关。具体而言,随着厚度的降低,表面孔的尺寸和密度增大(当厚度降低至13微米时,表面孔会演化为裂纹),锂与电解液接触的面积增大,锂补充的速率加快。同样,长循环测试表明随着CLC厚度的降低,全电池循环容量升高。然而,由于CLC-19的孔密度低,内部锂无法发挥,其循环稳定性与未补锂全电池相近。相反,对于Gr-CLC-13,由于活性物质的脱落,全电池在经过70圈循环后出现容量跳水。因此,该工作选用了厚度为16微米的CLC对石墨负极进行全生命周期补锂。通过对Gr-CLC-16进行静置-拔锂测试,可以得到CLC-16 中锂的利用率高达97%。
图3 不同厚度补锂集流体电化学性能
随后,对在电解液中静置不同时间的Gr-CLC-16进行XRD测试,结果显示随着时间的延长,石墨的锂化程度逐渐增大,这表明CLC-16中的锂是缓慢逐步释放的。锂的缓释是由于CLC独特的结构所带来的。在表面贴合预锂化中,锂合金完全暴露在电解液中,当电子转移通路不受阻时,合金中的活性锂在静置时会全部进入石墨。若此时采用5微米厚的锂箔进行全生命周期补锂,负极需要额外的1mAh cm-2的石墨来存储多余的锂,否则在充电过程中会有锂沉积发生。而对于CLC-16,大部分的锂合金被铜箔覆盖,锂箔只可通过表面微孔接触到电解液,锂释放速率大大降低。因此,当使用CLC-16对石墨进行全生命周期补锂时,全电池的N/P值仍为1.05,且循环过程中无锂沉积发生。全电池首次库伦效率只提升至92%,但由于锂在不断的从CLC中释放,电池的循环稳定性得到大幅提升:补锂全电池400圈后的容量保持率达到96%(对照组为80%)。
图4 CLC-16实现石墨负极的无损伤全生命周期补锂
补锂集流体实现硅负极安全无损预锂化
对于硅负极来说,表面贴合预锂化辊轧时的压力会使硅与锂迅速发生锂化反应。锂化过程中硅颗粒发生体积膨胀,给电极内部带来较大的内应力,造成硅电极破裂以及活性物质脱落等问题。同时,硅在短时间内的迅速锂化会放出大量的热量,使得极片温度在几秒内升高~20℃,对其规模化应用产生巨大的安全威胁。当使用CLC对硅进行预锂化时,铜箔隔绝了硅与锂合金的直接接触,避免了辊压时锂化所带来的电极损伤和热量释放,实现了硅基负极的安全无损补锂。
图5 补锂集流体实现硅基负极安全无损伤补锂
▍总结与展望
本研究系统地研究了表面贴合预锂化的缺点,并制备了一种含锂的复合集流体。在预锂化过程中,由于锂在接触点的溶解而破坏了必要的电子路径,导致大量的表面锂残留和低的锂利用率。这些残留物进一步破坏了界面的稳定性,一旦补偿的锂被耗尽,电池容量就会加速衰减。同时,负极的迅速锂化会产生热量,特别是硅负极的锂化产生的热量可以使电极温度升高20°,带来热失控风险。而CLC将LiAg封闭在铜箔内,有效地解决了这些挑战。它通过导电铜建立了稳定的电子路径,确保了石墨稳定的锂化路径。因此,CLC的锂利用率得到了大幅提高,达到97%。此外,CLC固定了不可避免的合金残留,消除了它们对电池稳定性的潜在不利影响。此外,还可以通过调节制备过程中形成的Cu层内Li+通道的大小和密度,从而调节锂的释放速率。这使得补充的锂容量会被及时消耗,而不需要额外的负极负载。因此,CLC实现了无损的全生命周期补锂,使LFP||Gr-CLC全电池在400次循环后保持96%的容量(LFP||Gr全电池400圈后容量保持率只有80%)。
▍文献链接:https://pubs.rsc.org/en/Content/ArticleLanding/2024/EE/D4EE02522A
文章来源:新威NEWARE
特别声明:本站所载图文内容均来源互联网,微信公众号等公开渠道,我们对文中观点保持中立,出于更直观传递信息之目的转载稿件,仅供参考。版权归原作者和机构所有,并不代表本网赞同其观点和对其真实性负责。如有侵权,或涉及任何第三方合法权利,请及时联系我们删除(微信:snan2109;QQ:906945059),我们会及时反馈并处理完毕。